SOFT SENSOR FLASH: un paso más en la transformación digital de Petronor
La Inflamabilidad en el refino es un parámetro de control de calidad clave para la comercialización de gasóleo. Se desarrolló e implementó un sensor virtual que infiere la Inflamabilidad en tiempo real a partir de otras variables con una precisión comparable al método oficial de análisis ASTM D97.
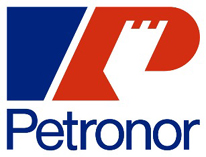
-
Actividad
Descripción de la actividad de la organización
Refino de productos petrolíferos y sus derivados, incluyendo el transporte, almacenamiento, distribución y venta de los mismos, con foco en el desarrollo de cuantos proyectos son necesarios para realizar la transformación digital y descarbonización de los productos.
Sector
Refino de productos petrolíferos y sus derivados
Nº de personas empleadas
975
Localización
B, San Martin, 5, 48550, Muskiz, Bizkaia -
Argumento
Antecedentes
La temperatura flash es un parámetro crítico de calidad para la venta del gasóleo, así como para la seguridad de su almacenamiento y transporte. Para el control de dicho parámetro se ha utilizado tradicionalmente una inferencia estática centrada en el uso de modelos de simulación rigurosos como apoyo al método oficial de análisis ASTM D97. Aprovechando la apuesta de Petronor por la transformación digital y las tecnologías 4.0, se propuso desarrollar nuevas aproximaciones basadas en tecnologías de inteligencia artificial (machine learning) para el control de este parámetro crítico
Reto
El reto consiste en desarrollar técnicas de inteligencia artificial que permitan mejorar la eficiencia del proceso productivo en base a la medición en tiempo real de la temperatura flash. Realizar un control preciso de dicho parámetro es clave para el proceso de fabricación y comercialización del gasóleo.
Razones para ser considerado un Caso Práctico de Innovación
Porque se han introducido exitosamente soluciones de inteligencia artificial (machine learning) que permiten controlar de manera precisa un parámetro clave de calidad de producto en el proceso productivo de la industria de refino, en base a información de variables disponibles en tiempo real y procedentes del mismo proceso productivo. Además, estas soluciones introducidas suponen importantes ahorros económicos para la planta de Petronor.
-
Descripción
Petronor (Grupo Repsol) es la mayor refinería de España, con un potencial productivo de 12 millones de t/año. La empresa obtiene productos derivados del petróleo para su aplicación en ámbitos diversos (gases licuados, naftas, querosenos, gasóleos, asfaltos, etc).
Precisamente, y con relación al gasóleo, uno de los parámetros clave de calidad para su comercialización se refiere al así denominado “temperatura flash” o temperatura de ignición que resulta clave en la seguridad del producto para su comercialización, almacenamiento y transporte. Dicho parámetro se controla de forma tradicional con el método oficial de análisis de laboratorio según ASTM D97, así como a través de una inferencia estática centrada en el uso de modelos rigurosos basados en relaciones termodinámicas y modelos de simulación.
En línea con la apuesta del plan estratégico 2018-2022 del grupo Repsol por la transformación digital como palanca de la eficiencia y sostenibilidad de los procesos productivos, la compañía se propuso desarrollar desde Abril a Septiembre del año 2020 un proyecto piloto innovador centrado en la transformación digital del proceso de refino. Para ello, se ha apostado por desarrollar un conjunto de algoritmos que, mediante técnicas de inteligencia artificial (machine learning), permitieran realizar una medición precisa o Soft sensor de la temperatura flash en tiempo real en base a información de variables disponibles en cada momento y procedentes del proceso productivo. De esta forma, el modelo de cálculo desarrollado es capaz de adaptarse a los cambios y a la operativa de la planta, además de capturar y obtener la información óptima en cada caso.
Para ello, la compañía ha dedicado importantes recursos humanos, monetarios y organizativos (una científica de datos y dos expertos de dominio, además de personal asignado al proyecto a media jornada en su duración total, 6 meses de trabajo de prototipado, validación y puesta en producción). Además, Petronor a través de su propia Unidad de I+D “Petronor Innovación” se ha apoyado en la ayuda del Centro Tecnológico Tecnalia, que ha aportado su valor como desarrollador tecnológico.
Desde un punto de vista organizativo, la innovación introducida ha supuesto un cambio importante en la manera de operar tradicional del control del proceso productivo, lo que ha supuesto un importante avance en la transformación digital de la compañía y de sus trabajadores. Está previsto que esta experiencia sea extendida tanto a otras unidades de tratamiento de gasóleos como a otras unidades de la planta para la predicción de nuevos parámetros operativos y de calidad, siguiendo para ello la metodología y conocimiento ya adquirido con esta experiencia piloto. -
Acciones
Las principales acciones realizadas han sido las siguientes:
1. Desarrollo, implementación y validación de una herramienta de inteligencia artificial (machine learning) para la mejora del proceso, a través del desarrollo de un Soft sensor para la medición de parámetros de calidad en línea. La herramienta tiene un módulo de clasificación de muestras, que evalúa su precisión y genera nuevos modelos de predicción cuando se identifica un nuevo patrón de comportamiento (aprendizaje dinámico).
2. Evaluación del error de la predicción del Soft sensor respecto de las muestras de laboratorio, usando para ello métricas estándares aceptadas por la norma internacional AST D97 (norma de referencia para la comercialización del producto).
3. Evaluación y análisis de los resultados obtenidos por parte de los expertos, para valorar la necesidad de realizar los ajustes óptimos en las condiciones de operación para un proceso más eficiente.
4. Integración y análisis de calidad de datos, preprocesado, estimación de decalajes, selección de variables, desarrollo de algoritmia, validación y puesta en producción.
A futuro, esta solución desarrollada va a ser extendida a otras unidades de tratamiento de gasóleos de la compañía. Está previsto además la creación de más sensores para la predicción de nuevos parámetros operativos y de calidad en otras unidades de la planta, siguiendo para ello la metodología y conocimiento ya adquirido con esta experiencia piloto. -
Resultados
Los principales resultados obtenidos son los siguientes:
• Los modelos desarrollados permiten ajustar la operativa sobre propiedades de producto clave en tiempo real y ejercer un control de proceso óptimo prácticamente la totalidad del tiempo. En este sentido, dichos modelos permiten dar información confiable el 94% del tiempo de operación, comparable al error de la norma estándar ASTM D97 para la comercialización del producto en estudio. Todo ello redunda en una mayor eficiencia de los recursos utilizados, además de alargar el ciclo de vida de la unidad y el catalizador empleado en los reactores.
• La tecnología empleada permite conseguir desarrollar modelos dinámicos que aprenden de comportamientos que están sucediendo en la planta industrial y los que irán sucediendo con el paso del tiempo. Así, el modelo se calibra de forma continua, sin necesidad de recalibrar el modelo offline, como se hace habitualmente.
• Desde un punto de vista económico, la implementación de la herramienta supone un potencial ahorro anual de 960k€ en la unidad de desulfuración piloto, lo que escalando este resultado al resto de la planta implicaría conseguir unos ahorros añadidos cifrados en 1.95M€/año por eficiencia de proceso. -
Contacto
Lucía Orbe-Guijarro
Testimonios
Lucía Orbe (Gestora de Proyectos de Innovación)
"Tener información precisa de la calidad de los productos en tiempo real permite optimizar el proceso generando productos de alto valor añadido de la manera más eficiente"Manu Nuñez (Director de Petronor Innovación)
“Si no hay innovación continua en los productos, en los procesos y en la gestión, no se generan las mejoras necesarias para dar respuesta a lo que la sociedad nos demanda en cada momento. Aplicamos estrategias de digitalización a toda la cadena de negocio” -
Soluciones relacionadas